Smart Warehousing: What are Smart Warehouse Systems?
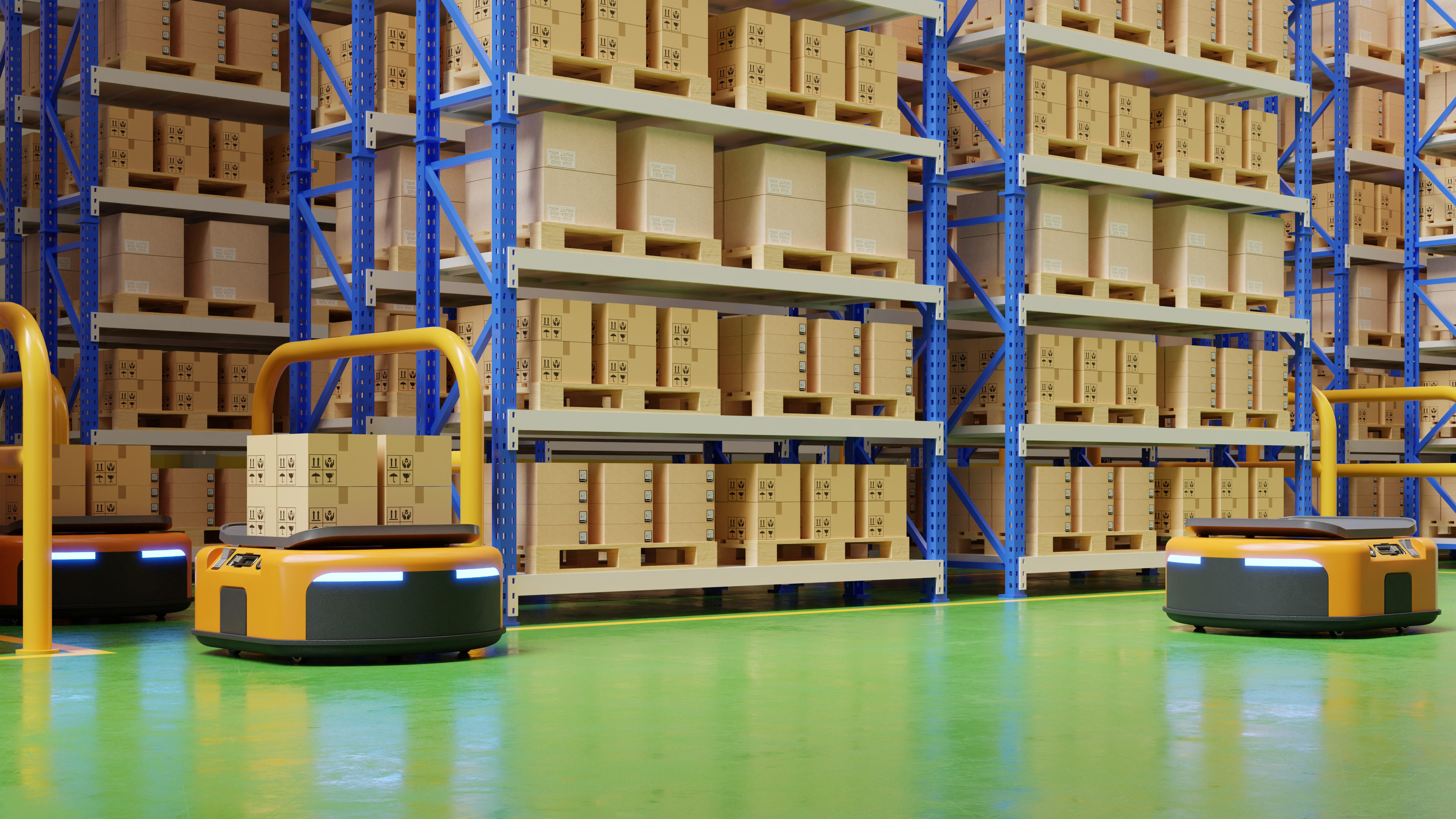
The future is now. That’s certainly what it’s starting to feel like anyway. While we may not have the flying cars from “The Jetsons”, and “Jaws 19” from “Back to the Future Part II” has yet to hit theaters, our technology is advancing rapidly. Automation is more prevalent than ever, making many of our jobs exponentially easier. Smart warehousing via warehouse management software represents some of the best examples of businesses embracing this new type of technology.
When considering a new warehouse system, it is important to feel out your options before making a choice. Our comparison guide can help get you on the right track and give you a better look at the vendor landscape.

Source : selecthub.com
What is a Smart Warehouse?
A smart warehouse is the culmination of warehouse automation (in other words, automating various components of your warehousing operations). Similar to smart homes, a smart warehouse is enabled with several automated and interconnected technologies. These technologies work together to increase the productivity and efficiency of the warehouse, minimizing the number of human workers while decreasing errors.
As Royce Digital explains, “In manual warehouses, we usually saw workers moving around with lists, picking products, loading them into carts and then delivering them to the shipping docks,” but in smart warehousing, “Orders are received automatically, after which the system confirms if the products are in stock. The pick-up lists are then sent to robot-carts that place the ordered products into containers and deliver them to workers for the next step.”
What are Smart Warehouse Systems?
Smart warehouse systems, then, are the result of the various interconnected warehousing technologies working together. They form a technological ecosystem where goods are received, identified, sorted, organized and pulled for shipment automatically. The best smart warehouse solutions automate almost the entire operation, from suppliers to customers, with minimal errors.
When considering smart warehousing, you should keep an eye out for a few traits that mark a successful smart warehouse system. Some of these traits are:
Agility
It’s no secret that warehousing operations are becoming more and more complex. To meet these complex needs, smart warehouses need to be able to shift gears and field the rapidly changing variables in today’s world. Your smart warehouse system should constantly attempt to optimize the travel of products from storage to shipment. Not only that, but smart warehousing operations should also be on the lookout for temporary storage opportunities and third-party logistics (3PL) providers in case of temporary stock overflow.
Staffing needs also need to be considered and implemented by your smart warehousing systems. The goal of a smart warehouse is to limit the need for on-site staff but to also be prepared to staff up during busy times of the year. A good smart warehouse will keep a cross-trained group of core employees in place for slower months.
Agility also comes in to play in regards to the various software used in your smart warehouse. All of your systems should be able to work with numerous platforms, sales systems and other warehousing functionalities. One thing to consider is the use of a software as a service (SaaS) solution, as these systems are becoming standards in many industries.
A SaaS smart warehousing solution usually comes with a lower price of entry that can be paid in monthly installments as long as you need the service. These services also save time by removing the need for massive on-premise software updates that are normally required.
Scalability
As the complexity of warehousing and supply chains continue to grow your smart warehouse should always have an eye on the future. Smart warehouses need to be ready to accept large influxes of product and new product releases at any moment.
This brings us back to another attractive quality of SaaS solutions. Adding new features to your smart warehousing systems can be difficult if you have an on-premise solution. In some cases, the entire system may need to be taken down while updates are completed which can lead to a major slowdown within the warehouse.
A SaaS solution does not struggle with this limitation. Updates can be completed on the fly and new inclusions can be rolled out without taking a hit to efficiency. Implementing a new feature only to have to bring in IT to fix unexpected issues is a headache no smart warehouse operator wants to deal with.
Data Visibility
As technology continues to progress, the visibility of data has become a must-have for most software tied to supply chain functions. This is very important today, as supply chains and warehousing operations become more complex, software solutions need to be ready to update and store data immediately. Customers and stakeholders want to be able to tap into the real-time data provided by your smart warehousing system and see where their product is right now.
Your smart warehouse should allow interested parties to be able to find what they want to immediately. If a customer has a choice between partnering with an operation that updates their data overnight or one that stays up to date constantly, you can bet on which one they’ll choose.
Not only is this aspect important when considering client retention, but data visibility also provides a host of useful information to the operation itself. Real-time data gives operators a bird’s eye view of the entire warehouse and how its various pieces are performing. If inaccuracies in inventory or delivery timing are cropping up, you’ll immediately know where they are originating from. This way smart warehouse operators can take action before things get out of hand and throw an even bigger wrench into the works.
Components
At its most basic, a smart warehouse is made up of a variety of interconnected technologies all working toward the same goals. Every piece of this puzzle has a job to do that keeps your warehouse running optimally. Here are a few examples of the many components you’d find in a smart warehouse:
Robotics
Humanoid robots that inhabit our science fiction shows and stories are still a long way off, but there are other types of robots that are almost as cool. Warehousing robots that you would see today mainly handle the picking and packing of goods.

Although simulated, this image depicts warehouse robots at work. source : selecthub.com
Usually resembling Roombas, your common warehousing robots automate the picking process by physically bringing product shelves to the human workers packing orders. Essentially, they’re automated, more maneuverable pallet jacks. They move faster than people can, move more goods at once and they can even identify the optimal route for picking up the necessary products.
Radio-Frequency Identification
Radio-frequency identification (RFID) helps organize and control inventory. RFID gets rid of old analog paper tracking methods in favor of tracking packages with digital tags. Radio waves are then used to transfer data to or between the digital tag and an automated scanning system, recording the product’s information.
RFID replaces old barcode scanners, where the barcode has to be precisely aligned with the scanner to identify it. Instead, RFID scanners can simply be pointed in the general direction of the package in order to identify it.
How does this help with inventory management? For one thing, since scanners don’t have to be precisely aligned, automated machines can be used to scan packages as they come in, identifying and counting how many of each type of good is received. In addition, these scanners can detect goods as they leave the warehouse during order fulfillment, ensuring that your inventory count is always accurate.
Artificial Intelligence
The use of artificial intelligence (AI) is exploding in every industry, not just in warehousing. The main reason? AI helps boost productivity while minimizing errors.
For example, AI helps warehousing robots find the most efficient route for picking products. It can also be used to determine the best box type for a shipment based on the type, number, size and weight of the products. Some warehouses have even been able to implement machines that can pack products, using AI to pack them in the most space-efficient manner.
Capabilities such as these are helping warehouse operations drastically reduce their operating costs. One of the biggest costs it’s reducing is the number of human workers. According to Cerasis, 30% of UK jobs will become automated by 2030, due in large part to the use of AI.
The Internet of Things
You’ve probably heard of the internet of things, or IoT, by now. If you want your smart warehouse to work correctly, you’re going to be relying on IoT. If you need a refresher, IoT involves several Internet-enabled devices communicating with each other and sharing data. In smart warehouse systems, this means that robots can communicate with all of the tech it needs to, including a warehouse management system (WMS).
An example of IoT at work in a smart warehouse management system starts from a warehouse receiving a product. As the shipment is received, an RFID scanner scans the tags, telling a WMS which and how many goods were received. The WMS then communicates with robots, informing them of where those goods should be stored on the warehouse floor.
All of this happens automatically and seamlessly, without losing any crucial information along the way. Without IoT, a human worker would have to complete each step in the process manually. This is prone to error, especially with the massive amount of information about each product that flows through these systems. But thanks to IoT, humans are all but eliminated from the equation, speeding up the process while drastically reducing errors.
Looking ahead, some are even beginning to prepare for an “internet of everything”.
Warehouse Management Systems
The use of a WMS is the cherry on top of all of your smart technology. A WMS solution has many uses, from gathering valuable data to helping users manage warehousing processes. This allows you to keep track of how efficient your warehouse’s day-to-day operations are and if you can improve on anything specific.

A WMS opens up a whole new level of warehouse optimization. Source : selecthub.com
Since most WMS solutions can collect real-time data and create visual reports, they help reveal any deficiencies in your processes. After viewing a WMS report, you can take appropriate action to fix any issues and get your operations back on track.
Implementation
The warehouse of today is starting to resemble a scene from a sci-fi movie — and we think that’s a good thing. As we continue on into the not-so-distant future, warehouse automation will become even more prevalent, and smart warehouse systems will dominate the industry. So not to be all, “The end is nigh!” for warehouses that don’t embrace smart warehouse management systems, but … the end is nigh.
It’s time to start implementing automation. We’re not saying that you need to buy and implement every piece of technology we listed above (not right away, at least). That would require a huge upfront investment that only the largest of warehousing operations could afford. Instead, start small and build towards automation. Start with just one of these technologies, and after a few years, add another. A few years after that, add another, and so on and so forth.
We suggest starting with a WMS. It’s one of the cheapest to implement, and by gathering and managing your warehousing data, it’s essentially the heart of a smart warehouse system.
Keep your operation’s requirements in mind when choosing a solution and you’ll be on the right path to selecting your perfect system.
Final Thoughts
Smart warehousing brings a significant amount of optimization to any warehouse operation. Automation is on the rise and will continue to be adopted by more and more warehousing companies, don’t fall behind!
How have smart warehouse solutions taken your warehousing operations to the next level? Tell us in a comment down below!
Source : selecthub.com