What is causing supply chain disruptions?
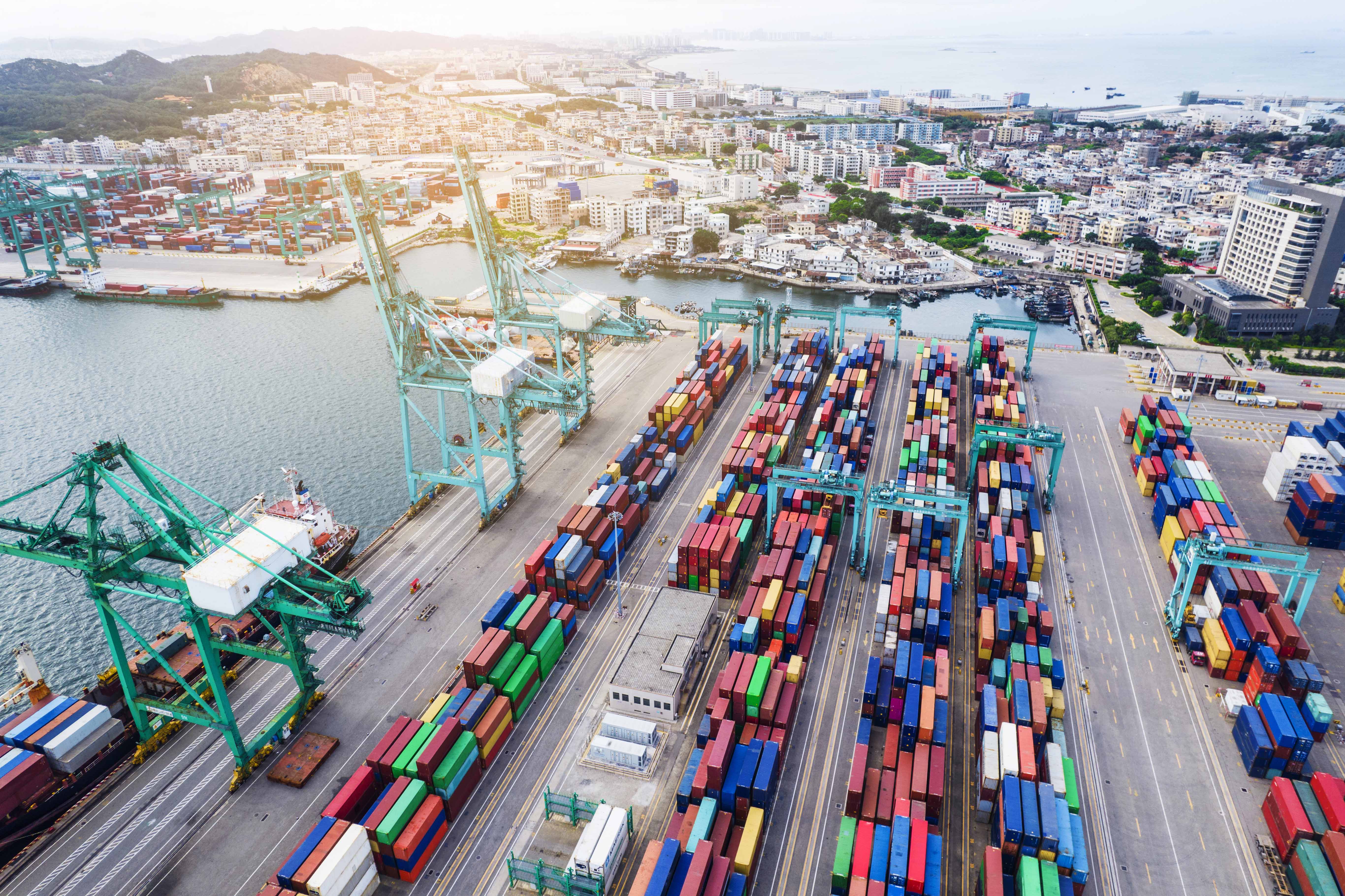

Jon Padfield
Editor’s note: This is the first in a series of columns for The Republic’s business section from local IUPUC Division of Business instructors.
By Jon Padfield
For The Republic
I am the faculty lead for the new Supply Chain Management Concentration at IUPUC’s Division of Business. While I have been teaching Supply Chain Management courses for several years, it was a topic most people didn’t think much about until the beginning of COVID-19 when we all began seeing something most of us were not accustomed to seeing – empty shelves in stores.
It began with shortages of toilet paper, hand sanitizer and a few other essentials but now, nearly two years later, we are continuing to see shortages of a wide variety of products. I recently had a conversation with an employee of a small, specialty grocery store in Indianapolis who told me they were struggling to find new sources for over 200 products they normally carry but are currently unable to purchase from their regular suppliers.
I frequently have people ask me what (or sometimes who) is to blame for product shortages.
This is not a simple question to answer, and it depends greatly on what product shortage they are talking about. California wildfires this summer in the Napa-Sonoma wine region devastated many square miles of vineyards and contributed to shortages of certain brands of California wine.
The toilet paper shortage in early 2020 was entirely different. While there was undoubtedly some panic buying/hoarding going on, there was a much bigger problem that most people never realized. Total toilet paper consumption in the United States is stable over time but it is sold in two different forms: small “residential rolls” that most of us buy at Target or Walmart and large “institutional rolls” that are frequently purchased for schools, office buildings, and factories.
At the onset of the COVID shut down in March of 2020, there was little demand for the large institutional rolls because nobody was going to work or to school and the demand for residential rolls dramatically increased because more people were spending more time at home. This sudden, unprecedented shift in demand required time for companies to adjust their production to make more of the residential size rolls.
A similar phenomenon occurred with companies that sell bags of flour. As restaurants shut down and more people were cooking at home, the demand for 50 lb. bags of flour dropped as the demand for 5 lb. bags of flour spiked.
However, the aspect of supply chain management that has received the most attention over the past few months has been the number of cargo ships sitting off the coast of California. I want to state unequivocally that there is no one root cause to blame for this situation. Instead, there are numerous contributing factors that have combined to get us where we are today.
Supply chains, just like any other chain, are only as strong as their weakest link. A common model of a supply chain includes “tier 2 suppliers” who sell parts or material to “tier 1 suppliers” who use them to create components for Original Equipment Manufacturers (OEMs).
OEMs then sell their finished goods to distributors who in turn sell those same finished goods to retailers who in turn sell them to consumers. There are many variations of the supply chain as some companies sell direct to consumers, but the general idea is that material flows from “upstream” suppliers to “downstream” consumers.
Today, many of the products we regularly purchase are either manufactured overseas or are manufactured in the United States using material or components imported from overseas.
When measured by volume, 99% of U.S. imports arrive by cargo ships but when measured by value, only 65% arrive by cargo ship. This is because high value items such as iPhones are normally imported by air rather than sea.
The total volume of global cargo transported by ships in 1990 was 4 billion tons. In 2019, that number had nearly tripled to 11 billion tons. Not all of that cargo was being imported into or exported from the United States so let’s just focus on the Port of Los Angeles. In 1990 the Port of Los Angeles handled 2.1 million TEUs (Twenty-foot Equivalent Units – literally a 20’ long by 8’ wide by 9’ tall container). By 2019 that volume had more than quadrupled to 9.3 million TEUs.
But this is only part of the story. Once those ships arrive at the Port of Los Angeles, they need to be unloaded. Today’s largest cargo ships such as Ever Ace or the HMM Copenhagen can carry approximately 24,000 TEUs. Hypothetically, if those 24,000 cargo containers were placed end to end on a train, it would be 90 miles long.
The other option for moving cargo out of the port is loading the cargo containers onto trucks.
According to the October 2021 “Critical Issues in the Trucking Industry” report, published by the American Transportation Research Institute, the number one issue for the fifth consecutive year is the national truck driver shortage and the shortage was recognized as a developing problem for at least a decade before it became the number one issue in trucking.
Source : therepublic.com