Moving Toward the Era of “Logistics 4.0”
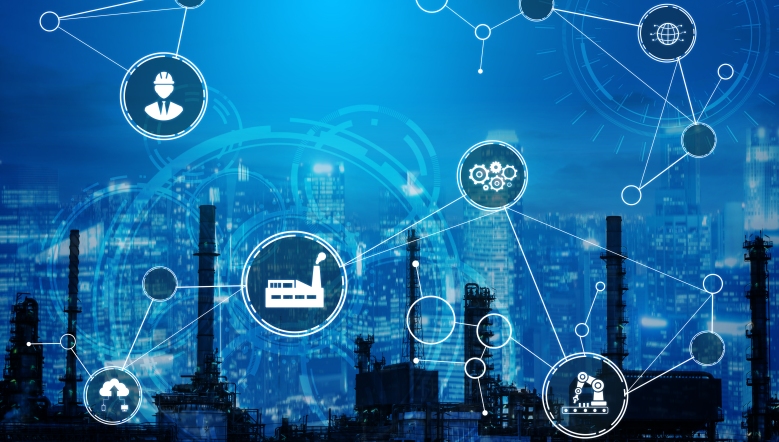
The emergence of Industry 4.0 prompted new challenges in the logistic domain, pushing consideration of technological changes such as a serious need for transparency in supply chains. These advancements will drive the transformation of logistics from Logistics 3.0 to “Logistics 4.0.”
The emergence of smart and intelligent technologies — Industry 4.0 — in the past decade has disrupted many industries and businesses. Global supply chain disruptions, capacity shortages, port congestion, increasing air freight rates and an ongoing pandemic have stressed shippers, ports, carriers and logistics providers during the past two years. Today, businesses must embrace smart technology to remain relevant in the market. The logistics industry, with its focus on enhancing customer service, must strive toward transformation, flexibility and agility in three key functional segments of logistics: Information flow from seller to buyer; product flow from seller to customer; and finally the cash flow from buyer to seller for the delivery of goods and services.
What is smart logistics and why now?
The emergence of Industry 4.0 prompted new challenges in the logistic domain, pushing consideration of technological changes such as a serious need for transparency in supply chains. These advancements will drive the transformation of logistics from Logistics 3.0 to “Logistics 4.0.”
Smart logistics is a system that can increase flexibility, adapt to market changes and bring the company closer to the needs of its customers. This will allow for improved customer service, production optimization and lower storage and production costs. Smart logistics will evolve in accordance with current technology.
The major purpose of smart logistics is to promote the intelligent networking of products and processes along the value chain, allowing it to use organizational processes more efficiently in the creation of goods and services to benefit customers. Industrial equipment, products and services that connect with humans and other devices will be used in smart logistics. The IoT, artificial intelligence and automation are enabling a new wave of manufacturing innovation.
Ongoing challenges with Logistics 4.0 transformation
Implementing Industry 4.0 is similar to process innovation. It comes with whole gamut of steps which pose a serious challenge to success. Key challenges usually fall into three broad categories – people challenges, technology challenges and process challenges.
People challenges are often associated with a lack of common vision and the understanding of a smart factory. Complexity arises from an attachment to legacy technologies and a perceived threat to established norms and competencies. The complex nature of Industry 4.0 systems makes it difficult to gauge future benefits, creating an uncertain business case. Logistics and supply chain companies have a hard time moving away from their traditional processes and work routines which affects the digital transformation journey and the tangible benefits it promises to deliver.
How to enable this transformative journey?
First and foremost the critical enabler for this journey will be the complete buy-in of executive leadership, recognizing the imminent need for the digital transformation of processes, systems and technology. Companies must develop a long-term strategy roadmap for technology and solutions and take a systematic approach to the adoption of cutting-edge methods and models that drive agility, flexibility and faster time to market.
Once leadership is aligned the transformation from a traditional culture to digital culture becomes easier and more agile. One of the first changes is to focus on developing digital talent. The entire workforce needs to evolve as the digital transformation process unfolds in phases. Also, it’s imperative that companies look toward a modular approach to technology. Dividing technological solutions into modules and delivering solutions in phases allows for the training of team members on solutions, helps build acceptance, and minimizes the stress of transitioning to new systems.
This journey requires foundational changes at several levels. The first is identifying connected technologies which drive a culture of digital inclusion, formalizing the implementation processes by applying a digital lens to map existing and upcoming technologies.
The next level is about driving the people, process and systems to gather structured data, analyze it and then share the information through creative channels. At this level, building an environment of collaboration and teamwork allows broader visibility of information and the ability to act on it.
The final level is building systems and processes for forecasting and implementing simulation systems or digital twins for testing, prototyping and optimizing the digital warehouses. Achieving maturity at this level consistently is what aids business to have better, predictable decision outcomes and to enable stronger supply chain predictability.
Source : eetasia.com